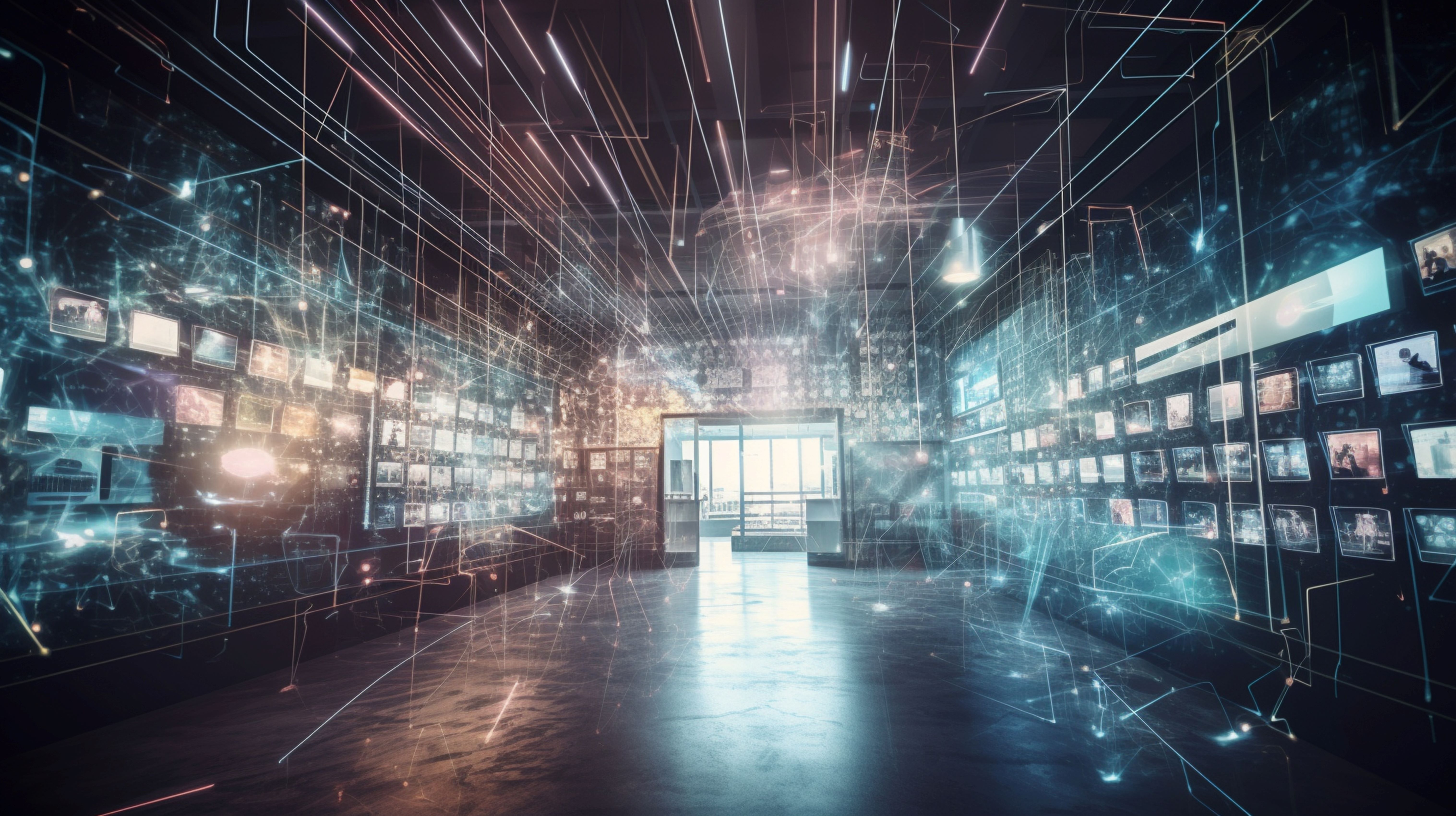
By Jens Bohnwagner, CEO, XSQUARE Technologies
Automation is now the linchpin of companies in the industries of manufacturing, production and intralogistics. The combination of advanced technology, the speed and precision of robots and autonomous forklifts increase productivity and build a safer workplace for employees. Contrary to the old age thinking that technology displaces workers from their jobs, employees can now upskill and take on higher-level roles.
These benefits justify the estimated warehouse automation market to reach US$41 billion by 2027 at a CAGR of 15% between 2022 and 20271. Conversely, it indicates that many warehouses are still manually operated. Since the last decade, only 15% of the warehouses have been mechanised, with 5% using sophisticated automation equipment and solutions2. Those partially automated warehouses now incorporate systems such as conveyors, palletisers, and wrappers in their operations, and they are mainly at the infancy stages of automation. As a result, they may still need to meet their automation goals despite the initial investment.
A successful journey of automation should lead to outcomes including optimised productivity that minimises operating costs, scalable operations, sustainability initiatives to reduce waste, better employee well-being and a higher level of job satisfaction. Importantly, automation also addresses the ongoing labour shortage issue.
So, what is a successful journey to a fully automated warehouse like? Firstly, a warehouse’s automation’s primary objective is to maximise storage space use. The increased demand for your services translates to the need for higher occupancy – simply because land shortage limits storage area expansion. It explains the need for taller racks, reduced aisle width and an inventory management system. Automation is handy when managing inventory stored on taller racks and maneuvering within narrower aisles. Autonomous forklifts can help with operations on taller racks, where safety is a concern. Workers can work alongside autonomous forklifts to identify and check high-value products and inventory confirmation tasks.
Secondly, interoperability is key. It means initiating the integration with all equipment within the operational environment, executing tasks across equipment that has been integrated and optimising throughput using various strategies, including pre-defined rules, machine learning and abstract priorities. The initial stages of integration and orchestration of equipment would require a warehouse control system (WCS) that provides a flexible and compatible solution to integrate all warehouse equipment. The equipment includes mobile racks, cargo lifts, autonomous forklifts, roller shutter doors and conveyors, to name a few.
Thirdly, automation should help companies increase productivity. The WCS will automate the operational processes in place, and, in some cases, the warehouse can operate around the clock without compromising your employees’ well-being. The WCS can orchestrate operations by leveraging real-time inputs from all automation technologies – meaning that a new shift work that relies on automation technologies is now an option. For example, autonomous forklifts can prepare outbound staging areas with goods, setting the morning shift workers up for the day. These just-in-time schedules will maximise the efficiency of assembly processes.
Lastly, automation paves the way for warehouses to play their part in creating a greener environment. Approximately 4 billion tonnes of carbon dioxide are emitted annually from the construction of new buildings worldwide3. By going higher with taller racks to optimise the warehouse layout, companies no longer need to constantly look for ways to continuously expand the square foot space of their warehouses as they scale their business. In the long run, it could also help businesses achieve financial and environmental sustainability, particularly as many countries start to consider taxing emissions. Efficient routing paths and narrow aisles also requires less energy compared to manually operated warehouses.
How do we begin a successful journey of automation?
Step 1: Define your needs
It is paramount for companies to spell out their unique set of operational requirements and gaps that they have identified in their current operations. As there is no one-size-fits-all solution to unique problems, businesses must communicate their challenges to experts in the field of warehouse automation. The automation solution provider must also have the skills and knowledge to diagnose the company’s unique issues and identify blind spots that AI and robotics can resolve.
The switch to intelligent warehouse solutions should be a strategic process of maximising throughputs with minimal effort. In the long run, it needs to be scalable, and the solutions must also be sustainable and environmentally friendly. It is vital to find ways to integrate existing warehousing solutions with the new investment in warehouse automation so as to keep costs at a minimum.
Step 2: Customise the solution
The best solution is customising solutions to a company’s needs and to maximise productivity without compromising safety. Safety is key when companies are increasingly working towards a future where humans and robots work harmoniously.
With advanced technologies, modern autonomous forklifts operate safely in mixed environments. A wide range of sensors is installed on the autonomous forklifts to detect humans or other obstacles and avoid them.
Step 3: Implement solutions that have been tested and executed for results
It is essential to do homework for your provider’s success and failure stories, as they are learnings for a company. An in-depth analysis should take place to minimise or eliminate potential risks.
Pioneering green logistics in Asia through automation
In Singapore, XSQUARE Technologies supplies Katoen Natie, an international logistics service provider and port operator with a fleet of autonomous forklifts. XSQUARE started with a single autonomous forklift for Katoen Natie in 2019. Since then, we have supplied the Belgian logistics firm with four additional autonomous forklifts at its logistics terminal that runs on solar power.
As more industries have started utilising automation to build smooth and efficient workflow, it is crucial to adapt to this ever-changing world. There are many benefits to implementing intelligent warehousing solutions into one’s facility. Companies should look at their processes, invest and implement intelligent warehousing solutions to promote interoperability of existing and new solutions.
[1] https://www.thelogisticsiq.com/research/warehouse-automation-market/
[2] https://www.robotics247.com/article/logistics_robots_ai_vision_offer_more_robust_warehouse_ecosystem/technologies
[3] https://psci.princeton.edu/tips/2020/11/3/cement-and-concrete-the-environmental-impact
As published in Industrial Automation Asia. Read here: https://iaasiaonline.com/ebook/2023/Apr/html5/index.html?&locale=ENG&pn=53
Supercharge Your Warehouse Today
Discover how intelligent automation solutions can revolutionise your business operations